Welcome to Fern Lane!
The Ecology Action Centre is located in an award-winning eco-renovated century-old saltbox style home in the North End of Halifax. Our office was renovated in 2016, increasing office space by 50 per cent while reducing energy consumption by 65 per cent. As of 2017, it is considered to be the most energy-efficient commercial office retrofit in Canada.
Our renovation has received a 2018 Canada Green Building Award from Sustainable Architecture and Building Magazine, a 2018 Bright Business Innovation Award, and has been named one of Canada’s Clean50 (www.clean50.com) Top Projects for 2019.
We strive to make our office a welcoming and inspiring space for community members, volunteers, and staff to connect, learn, and work together.
How we got here
In 2005, the EAC bought an old house on Fern Lane in Halifax’s North End. It took ten months and hundreds of volunteer hours to make it a beautiful home and a public demonstration of a green office building. Our showcase building inspired hundreds of property owners and builders to make greener choices.
Almost a decade later, we outgrew our home. The number of staff, volunteers and members at EAC had more than doubled, and our need for more space had become urgent! After weighing all the options, we decided to stay in this neighbourhood and expand the building.
We added a third storey and changed the layout of our main level to be more welcoming and accessible. We also made considerable improvements to the entire building's exterior shell to increase efficiency and comfort.
We celebrated the Grand Opening of our renewed Fern Lane office building on Earth Day, 2016!
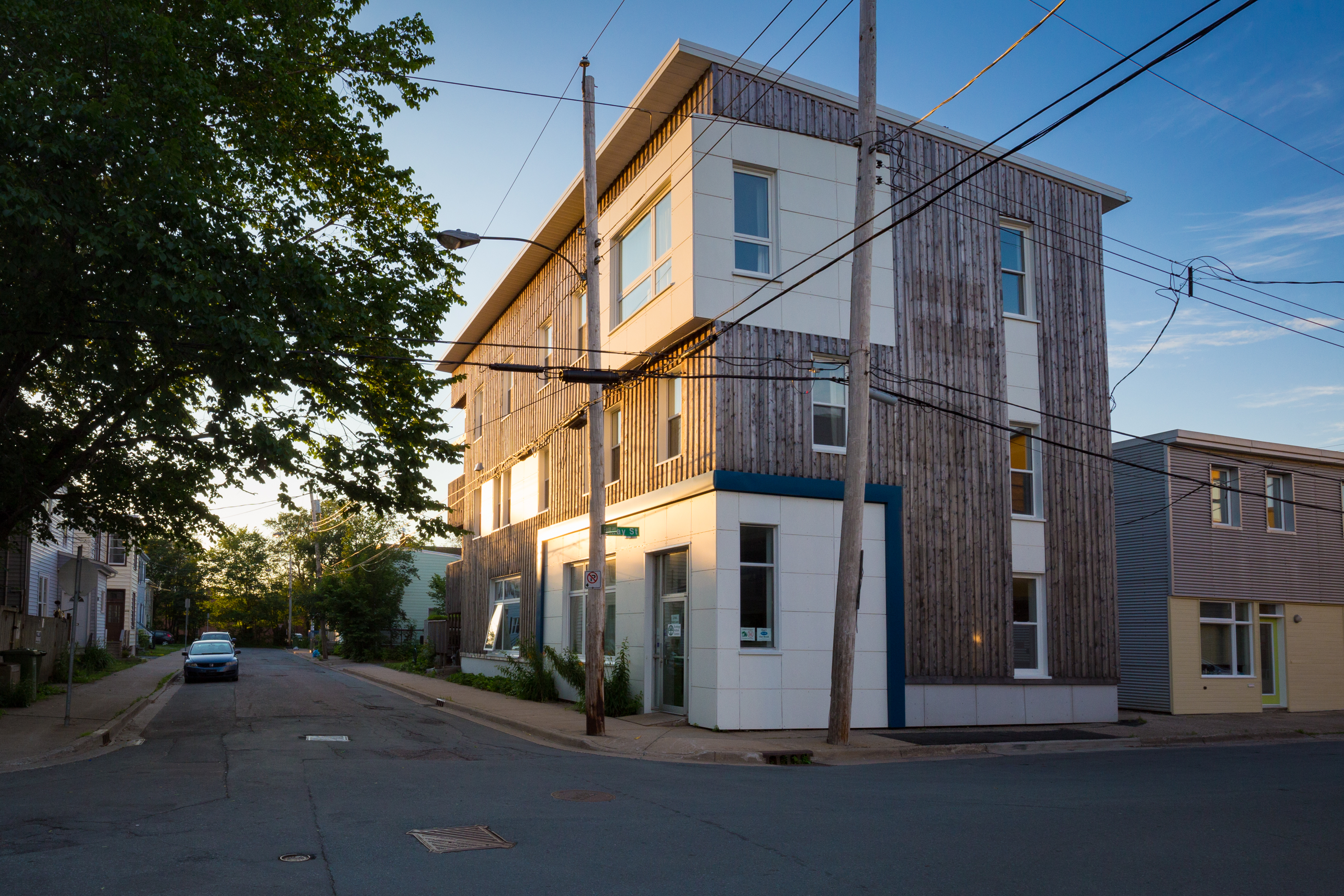
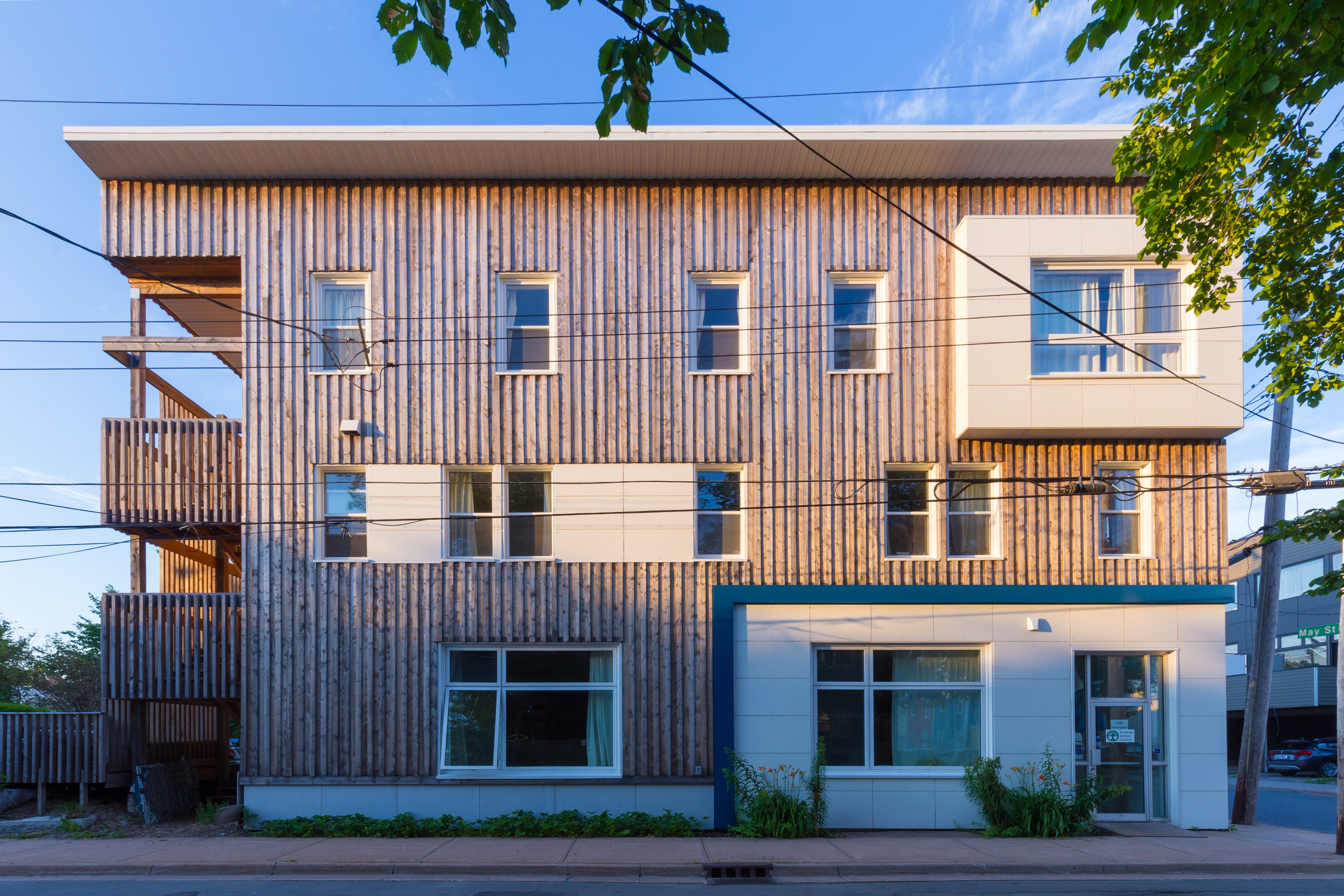
Renovations
2005 Renovation
2005-2006 Renovation
In 2005, the EAC bought a 90-year-old house on Fern Lane in Halifax’s North End. It was a typical North End Halifax “salt box”, rectangular in shape with a very slight slope in the roof. The building was approximately 3000 sq ft, almost double our previous space on Argyle Street in downtown Halifax. The following year, more than 150 volunteers have helped us transform our Halifax home into a 'green' office.
This was the first of two major renovations we did with our building – scroll down to learn about our 2015 renovation! Read on to hear stories from our 2006 renovation and learn about the decisions we made along the way.
The Beginning
The renovation was guided by Peter Henry Architects, the EAC Home Committee and Archnet Home Build and Renovate. The first floor had been renovated in the 1980’s while the second floor contained many original elements of the building, including trim, a cast iron bathtub and a slate fireplace. We completely altered the building layout, moved walls, stairways and added new windows.
Energy Conservation
We focused on improving energy efficiency through insulation to prevent heat loss, installation of a solar in-floor radiant heating system, and an increase in day-lighting as well as installation of energy efficient lighting. We also installed a heat recovery ventilation system (HVAC) to ensure that heat is not lost as fresh air is brought into the building.
Construction Material
We used local products, sustainable harvested wood, recycled and non-toxic products wherever possible. Many of our original choices such as straw board were ruled out because of availability and transportation costs.
The bookcase pictured on the right was constructed entirely of Forest Stewardship Council-certified, sustainably grown wood from Windhorse Farm.
Building Principles
The following principles were developed to guide decision-making in our own eco-renovation so that we could ensure that all decisions were consistent with our environmental and social values. We encourage you to consider this list as a start to setting out your own principles prior to starting your eco-renovation.
How will we prioritize green material procurement and use?
- Reduce material use
- Reuse what is in the building to the greatest extent possible
- Reuse materials either from other building sites
- Use recycled materials when possible
- Use natural materials, especially when using natural products means reductions in off gassing and improved indoor aid quality
- When new materials are required, choose locally produced products
- When there are no local producers, purchase from the closest supplier
- Follow LEED guidelines for products
- Choose materials that are made in Canada above other products
- Consider full life-cycle energy costs when choosing products
How will we determine supplying companies?
As a general rule of thumb, EAC will avoid purchasing products from companies that our campaigns actively engage in. We will assess this on an ongoing basis, and anticipate that our procurement philosophy will generally limit any conflicts of this nature. We will also support companies within the community, that reduce our need to travel to obtain necessary building supplies.
At what cost do we go out of the way to support locally produced materials?
The overarching EAC mandate is to create sustainable jobs for Nova Scotians, we would go to lengths to support local if indeed it is the best choice, from a longevity and reusable point of view.
Accessibility
We prioritized the transformation of Fern Lane into an accessible work place, adhering to Barrier Free Design Guidelines during construction.
Our first floor was made wheelchair accessible for a full range of office functions including the kitchen, copy room & mail room, two meeting rooms and all office spaces. High contrast wall and floor finishes were chosen for the visually impaired. Our back entrance is accessible from a ramp and deck, and we added an accessible washroom on the first floor.
Insulation
Our building had blown in insulation in its exterior walls, which was done in the 1980's. Despite this, results of a home energy audit, donated by the Clean Nova Scotia Foundation, showed that our building scored a 16 out of a possible 100 – with 0 being the outdoors, and 100 being a completely energy efficient, off-grid building.
New homes should be built to at least R2000 standards, with walls insulated to R-20 and roofs to R-40. The R–value relates to the thermal resistance of a material. During the renovation process, insulation choices were discussed extensively. The range of natural insulation products is great, but cost and local availability had to also be considered. We used a combination of materials, to achieve an R value of ~20 for all walls.
We added to the existing cellulose by an additional 2 inches of Styrofoam rigid board to all exterior walls. The product we used was called TrueFoam and is manufactured in Burnside Industrial Park in Dartmouth. Unlike many rigid foam boards, TrueFoam does not use CFCs or HCFCs. In areas where we had to replace the cellulose, we used formaldehyde-free fibreglass bats.
The roof had been un-insulated. We added blown in cellulose as well as TrueFoam for R-values that ranges from 39-57. Following insulation, all walls were sealed with a vapour barrier.
A second energy audit showed that we had tripled our score to receive 48 points. We will continue insulating the basement to receive a final score upwards of 53 points.
Energy Efficient Lighting
The best way to save energy on lighting is to design a building that makes the best use of daylight. We created ten interior windows on the east side of the building so that light could penetrate from the south and west sides into the interior of the offices. Unlike our previous office space, lights are rarely on during the day at Fern Lane.
Overhead fluorescent lighting was added, and each desk or workspace was given a task light equipped with a 15 watt fluorescent bulb.
Floor Finishes
We covered our in-floor, solar-powered radiant heating system with 2 inches of concrete intended to slowly radiate heat which keeps down the overall temperature in the building, and thereby conserves energy.
The concrete flooring was treated with Kemiko Concrete Floor Stain, and then Rembrandt Wax to provide a durable, low-maintenance surface. The acid used to treat the flooring has a surprisingly low environmental impact; it can simply be neutralized with baking soda upon removal.
Garden
A garden was designed and installed by students under Kim Thompson's direction at Dalhousie's Faculty of Architecture. The intent of this garden was to be a demonstration for organic gardening and composting. Raised beds allow universal access to vegetable and flower gardens.
Heating System
We added 2 rows of 6 solar panels to our roof. The panels are recycled, and were refitted by Thermo Dynamics Ltd in Dartmouth, NS, one of the world's leading developers of solar technology. The system was installed by Dr. Solar. These panels became the primary heat source through solar energy distributed through radiant in-floor heating.
The panels use sunlight to heat water by heating a metal Sunstrip that in turn heats a glycol solution (a mixture of antifreeze and water) that is then pumped through a heat exchanger in the basement. The pump is run by a small photovoltaic panel. The heat is transferred to pipes filled with water, which is then heated and circulated throughout the building, warming the concrete floors. The floors act as a thermal mass, collecting and holding the heat.
We also installed a small electric boiler to supplement the heating system. The split between solar and electric was expected to be 60/40 at the time of installation.
Indoor Air Quality
Throughout the renovation, we were very careful to avoid products and materials that are known to off gas and contain substances such as glue and formaldehyde. No OSB board was used, and instead we used sheathing donated by Veridity Products as it uses 95% less glue than conventional sheathing products.
In the finishing stages, we used no MDF or particle board. We made a concerted effort to replace our old particle board desks with solid wood desks and no new desks or chairs, that tend to contain fire retardants, were purchased. No carpets were installed in the building and all old carpets were removed.
Keeping staff and volunteers healthy is extremely important to us. Because of the scale of renovation, we were required by building code to install a ventilation system. The code now requires this because many air tight homes were being built with little opportunity for air exchange. These buildings often included materials that off-gassed and have resulted in human health concerns. A ventilation system ensures air exchange throughout our building. When it is too cold for the windows to be open and the ventilation system is in full force, an HVAC system efficiently transfers heat from the outgoing warm air to the incoming cool air.
We have also placed many indoor plants throughout the space to improve air quality by absorbing air pollutants.
Material Reuse
One of our guiding principles was to ensure that as little material as possible was taken to the landfill. With conventional renovation projects, up to 25%-50% of the original biomass of a building can end up in the landfill depending on the scale of renovation. In order to avoid this, EAC has worked hard to re-use and recycle as many materials as possible. We carefully sorted all of our construction waste.
Much of the plaster from the original building was removed and 9.3 tonnes were taken to C&D Recycling. Old plaster is made from lime and horse hair, and is biodegradable. All wood that was not reused in the building was taken to a welding shop and used to heat the building over the winter.
Lath removed from the plaster & lath walls was broken into small pieces and many, many people picked it up to use for kindling. Longer pieces were saved and continue to be used creatively to create pea trellises. All metal removed from the building, including t-bar from the dropped ceiling, and copper and lead pipe from the plumbing system, was recycled.
Extra TrueFoam insulation was inserted into interior walls to provide additional insulation and soundproofing. Many items, such as reusable t-bar, acoustic panels, old wall panelling, reuseable cellulose insulation, fluorescent lighting, electric baseboards among other things were posted on HRM Freecycle and reused by Freecycle members.
Sustainable Transportation Infrastructure
The Ecology Action Centre aims to be a model for other organizations by demonstrating sustainable workplace transportation infrastructure.
When the building was first sold, neighbours were worried that a new business would mean more traffic and less available parking on the street. In our 2006 renovation, we did the opposite of the vast majority of commercial properties, by reducing the available parking spots from 4 to 1. This gave us more room for outdoor meeting space, compost demonstration, and urban food production.
Bike racks were added to provide parking for up to 30 bicycles. A solar-powered, low-flow shower for those extra-long commutes was also installed.
Wall Finishes
Kim Thompson created a variety of incredible natural wall finishes on walls throughout the building. These finishes were extremely cost-effective, chemical-free and brought a natural elegance to the building.
Click here to see and download full recipes for some of the finishes used!
Most walls were painted a variety of natural colours to enhance light from the windows and create a refreshing atmosphere. Some of our wall paints were manufactured in Fredericton, New Brunswick by Eco-House, while others were a home-made clay variety. The difference from conventional paints was incredible. Even after two weeks of constant painting, there were no odours in the building.
The paint is a mineral based paint that absorbs into new drywall, rather than coating the surface like latex or oil based paints. Wood was finished with zero VOC Harmony paint from Sherwin Williams and paint for the bathrooms was purchased from Boomerang, a company that sells reconstituted latex paints that are mould resistant.
Water Conservation
Our initial goal was to reduce our water use by 75% over conventional offices and particularly over our past office. We installed a six litre toilet downstairs (most toilets are 13L) and a dual flush (3L/6L) upstairs. We also installed a waterless urinal which was sold locally by Green Pea.
We added low flow taps in the bathroom, kitchen, and shower.
One of the best ways to save water is to ensure that it is not wasted – that taps are not left running, toilet flushing is reduced and watering of plants is done by water collected off the roof instead of from the tap.
The building is plumbed so that in the future we can easily install a cistern to store rainwater collected from the roof. This water can then be used in our garden or for flushing toilets. This will reduce the storm water run-off from the building, and ultimately be less of a burden on the planned sewage treatment plant.
Our one parking spot is paved with Grass Crete – so that water can permeate back into the ground, instead of simply running into the street and down the storm drains.
In order to do our bit to clean up Halifax Harbour, we discourage flushing of any plastic products, such as tampon applicators. We use only biodegradable cleaners and properly dispose of paints and solvents.
Our water conservation strategy is a phased approach.
Moving Day
On May 1, 2006 we settled into our very own, eco-renovated home at 2705 Fern Lane. It became a working demonstration of a green renovation, and we began to give tours of the building to the general public.
Almost a decade later, we outgrew our home. The number of staff, volunteers and members at EAC more than doubled, and our need for more space became urgent! Read about our second renovation, which added a third storey to our building and further improved our energy efficiency, below.
2015 Renovation
2015 Next Level Renovation
Almost a decade later, we outgrew our home. The number of staff, volunteers and members at EAC more than doubled, and our need for more space became urgent!
In 2013, we began carefully considering options for growth. We soon reaffirmed our commitment to Fern Lane and to continued investment in this neighbourhood, this building and this community. As a result, we decided to embark on a major renovation and expansion project.
Our goals for our second renovation included creating a larger working space, making the building more accessible and welcoming, maximizing our energy efficiency, and creating a superb demonstration of a green building retrofit.
Design
In September 2014, we began working with Solterre Design and Tekton Design + Build on designs for the renovation. The team was tasked with providing the EAC with a green building while comfortably housing its ever-expanding number of staff and volunteers.
Check out the schematic drawings for this renovation here!
We considered a few schemes for the renovation. The options included clearing the site and building new, and various ways in which the existing building would be kept. The EAC’s Fern Lane home dates back to the late 1800s, when it was built for residential use. For all the charms Victorian-era buildings can provide, they can pose an equal (if not greater) number of problems for owners.
But Solterre Design co-founder Jennifer Corson had a strong interest in salvage. And after extensive budget consideration for the varying options, it turned out that keeping the existing building gives the EAC more bang for its buck. An all-new construction was the most expensive option and also the option providing the least amount of office space. Accordingly, Corson explains, this combo made a new construction a non-starter for the EAC.
After investigating multiple construction and design solutions, we decided to build a third storey (!) on our existing building, upgrade our foundation, change the layout of our main level to gain a more welcoming street level presence, and make improvements to the entire building's exterior shell to increase efficiency and comfort.
But potentially the most important aspect of keeping the existing building is the project’s ability to serve as a teaching tool.
“You’re seeing an example of what can be done with a 100-year-old wooden structure in Halifax,” Corson says. “If we’d cleared the site and put up a new efficient commercial structure, that’s not really playing out as an example.”
Next Level Mural
For our 44th anniversary, artist Jeff Domm created a beautiful mural showcasing endangered and lesser known Nova Scotian species for our board room. That mural was made as a fun way to track the progress of our capital campaign. See the mural in progress in the videos below:
Thanks to contributions from our members and the broader community, we were able to fundraise the money needed for our Next Level Renovation, more than $300,000.
You can learn about each creature featured in Jeff’s mural HERE.
Under Construction
We began construction in May 2015 on an extensive renovation that blended new construction. Here are a few of the features of that construction work.
Volunteer Engagement
Volunteers played a critical role in the creation of our #EACNextLevel building. In 2015, we held a series of “Work Parties”. Over 1,800 hours of volunteer time was been donated to this project thanks to an extraordinary community of supporters passionate about the environment. Volunteers have helped with everything from demolition to painting and clay plasters.
We also received help from the Parker Street Carpenter’s Assistant Skill Training Program. They lent their skills (and learned some new ones) in the renovation of the EAC’s Fern Lane building. The non-profit program (which closed in 2015 due to funding cuts) worked with those who faced barriers to employment to provided training and certifications necessary to find and maintain entry level jobs in the construction sector.
Participants helped us demolish several walls, as well as a ceiling and a chimney! We were very happy to get some extra skilled workers to contribute to our project, and to be part of such an important program.
Salvaged & Sustainable Materials
Local company, CarbonCure, helped us fill in old window openings in our foundation using 60 concrete blocks supplied by Shaw Brick. The blocks have a different chemical makeup from normal blocks thanks to the addition of 13 grams of carbon dioxide per block.
Here’s the oversimplified version of the process: waste carbon dioxide is supplied by industrial gas suppliers. It’s added to the concrete mix as a gas, a chemical reaction occurs and the carbon dioxide solidifies and is evenly distributed throughout the block. The end product looks the same and weighs the same as regular masonry blocks.
We salvaged an interesting array of materials including floorboards from the existing building which became a feature wall in the boardroom, beautiful old doors and light fixtures from former Dalhousie residential buildings that were being demolished, and 400 steel door cut outs for use as insulation.
The steel door cutouts were installed under our foundation by the crew of Tekton Design + Build, EAC staff and volunteers. They were donated by Peter Kohler Windows and Entrance Systems. It was a win-win for both parties. Kohler was able to divert its excess material from landfill and the EAC obtains the perfect pieces for basement insulation (at the best possible price).
Here's a quick rundown of the cutouts and why they’re such an amazing score:
- The “cutout” is the piece of an insulated steel door which is cut out when a window is installed.
- They’re ideal for insulation under concrete because they’re essentially a sandwich of insulating foam between steel skins, tough enough to allow volunteers to walk on them during installation without getting warped.
- The cutouts are rated R14 in terms of insulation value. (The higher the R value, the greater the resistance the material poses to the movement of heat.) The recommended insulation value for basement foundations is R21.
- The EAC’s cutouts measure roughly 2.5’ by 5’ apiece. Based on that size, the 400 cutouts will provide a double layer of cutouts prior to pouring the concrete foundation.
Energy Efficiency
Energy Efficiency was a top priority for our green renovations. Energy consumption from buildings is a big contributor to global warming. While our renovation added 50% more space, it is projected to have a 22% reduction in energy use.
Natural Plasters
100% of the walls feature natural wall finishes that are made with local materials including clay, sand and straw. These finishes are beautiful, functional, and free of volatile organic compounds (VOCs).
Third Floor Goes Up!
In August 2015, we started building the new third story of our Fern Lane home. We used an interesting and strategic process of building the whole third floor over the existing roof and making it weathertight before removing the old roof.
One of the big advantages of this method is that the building remains weathertight through the whole process, and the framing goes up really quickly.
During this time we also completed the interior stairwell, started collecting great salvaged materials, framed the new boardroom, and added exterior insulation for the foundation.
In the Meantime
While our office was under renovation, we moved our daily operations up to the seventh floor of 1888 Brunswick Street. With the hard work of our staff, the passionate support of our volunteers, friends, and allies, and the warm welcome of our new neighbours, our time in Halifax’s downtown was as busy as ever!
We hiked, biked, swam, and canoed across Halifax with our Hike the Greenbelt project. We held three Member Appreciation Events, our second annual Perfect World fundraiser, and a Living Shorelines planting day.
We took action on climate change and energy efficiency, environmental racism, fisheries management, and offshore drilling. We took the Federal Government to court over genetically modified salmon. Our Energy Coordinator Catherine Abreu attended the United Nations Climate Summit in Paris.
Long story short, it was an eventful seven months. We were thankful to Queen Square Development Ltd and Linda Harrie of Colliers International for helping us find our excellent temporary home and everyone else who helped make the transition possible.
Choosing Sides
Every construction project poses questions in terms of building materials:
- “How will it fare against Nova Scotian winters?”
- “Does it compliment the other parts of the building?”
- “Can we afford it?”
Choosing building materials for the EAC’s refurbished home lead to even more pointed questions. Our renovation was not simply a way to make Fern Lane bigger and better – it was about improving a great old building in accordance with EAC principles.
Collaborative discussions between designers, builders and EAC staff and volunteers helped determine the building’s exterior appearance. Budget and durability were key considerations, but three additional concerns were raised during these discussions:
- We want to support a local business;
- The wood used should be as local as practically possible; and
- The wood used should be harvested in a sustainable manner.
In the end, the EAC chose to work with Jeff Amos, proprietor of Amos Wood. Amos supplied reverse board and batten siding composed of knotty spruce. The wood comes with a 25-year guarantee (once EAC volunteers apply stain).
The choice couldn’t have been any more local. When visitors and passers-by admire the product, we can point them to Amos’s nearby storefront on Agricola Street. But Amos Wood is so much more than just a local option – it’s a small business using local lumber and sustainable harvest practices, headed by someone whose ideals go hand-in-hand with the EAC’s.
As for Fern Lane’s existing wooden shingles, they were covered with an air & weather barrier, which will itself be covered with a vapour-permeable exterior insulation. This ensures the walls can “breathe”, allowing any moisture in the walls a path back outside.
Moving Day
On moving day, FROGBOX Halifax loaned us seventy-five of their high-density polyethylene reusable boxes to transport our stuff. These boxes –which can be rented from the company– are reused hundreds of times and are easily recyclable at the end of their life cycle.
Cardboard boxes aren’t often reused, and if they are it’s generally less than three times. Cardboard can of course be recycled, but on top of the energy required to turn it into new products, inevitably some of the cardboard will end up in landfills, requiring the harvesting of new materials.
After four hundred uses, each FROGBOX produces roughly two hundred and eighty-two MTCE (metric tons of carbon equivalent) less than cardboard boxes reused three times.
On January 25, 2016 we moved back to our beloved home on Fern Lane!
Next Level Mural
Next Level Mural
We love our environment and all the plants, bacteria, critters and animals which make up our beautiful diverse landscape that is Nova Scotia, so we decided to make a mural with artist Jeff Domm for our newly renovated office space with over 44 different species in tribute to our 44 years of EAC!
The mural also helped us during our Next Level capital campaign, which allowed us to renovate our office space. With every $1,000 we raised for our EAC Next Level campaign, we flipped over one piece of this puzzle, to slowly reveal the beautiful mural underneath.
With your help, we raised $301,564!!
The puzzle is now complete. Come visit the mural in our newly renovated community space. Here are some details on the species in the mural!
Learn More
- FERN LANE ENCYCLOPAEDIA – A more in-depth look at the green building materials and techniques we used during our renovation.
History of EAC homes
-
Private house on Carleton St. (1971)
- Forrest Building, Dalhousie University (’71)
- The Roy Building, Barrington St. (fall '86)
- Veith House, North End Halifax (April '89)
- 1553 Granville St. (early '95) (just across from current MEC)
- 1568 Argyle Street (June '96) (Pizza Corner)
- 2705 Fern Lane (April '06)
Book a Tour:
We love taking individuals and groups on tours of our office to learn more about green buildings and the specific techniques we used here on Fern Lane. Email joanna@ecologyaction.ca or call 902-454-5226 to arrange a time for your tour!